

The BUBBLEDECK system offers a groundbreaking solution for modern construction by reducing unnecessary concrete from the neutral axis of floor slabs, which does not contribute to structural performance. This innovative method leads to a significant reduction in dead weight, enhancing efficiency and sustainability.
​
At the core of the BUBBLEDECK system is a patented integration technique that combines air and steel. By incorporating recycled plastic spheres as void formers within the flat slab, the system reduces the slab's dead weight by at least 30%.
​
This design innovation allows for greater flexibility, enabling wider spacing between columns. The BUBBLEDECK system also eliminates the need for beams by utilizing a flat slab construction that spans in two directions, directly connecting the slab to in-situ concrete columns.
​​The result is a more efficient, cost-effective, and sustainable construction process, delivering substantial benefits in both design flexibility and resource savings.

The engineering solution that radically improves building design and performance while reducing the overall costs.
DESIGN CONCEPT
The BUBBLEDECK system is based upon the patented integration technique - the direct way of linking air and steel. By adapting the geometry of the ball and the mesh, optimised concrete construction is obtained, with the simultaneous maximum utility of both moment and shear zones.
​
The construction literally creates itself as a result of the geometry of two well-known components: Reinforcement and hollow plastic balls. When the top and bottom reinforcement are linked in the usual way, a geometrical and statical stable BUBBLEDECK unit evolves.
​
The reinforcement catches, distributes and locks the balls in an exact position, while the balls shape the air volume, control the level of the reinforcement, and at the same time stabilise the spatial lattice. When the steel lattice unit is concrete, a “monolithic” biaxial hollow slab is obtained.
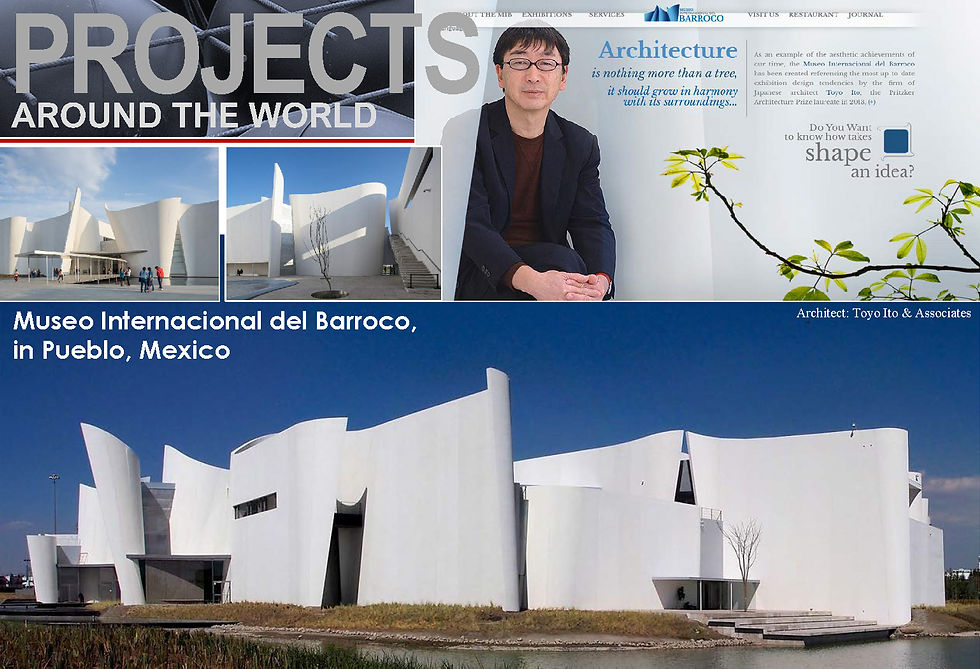


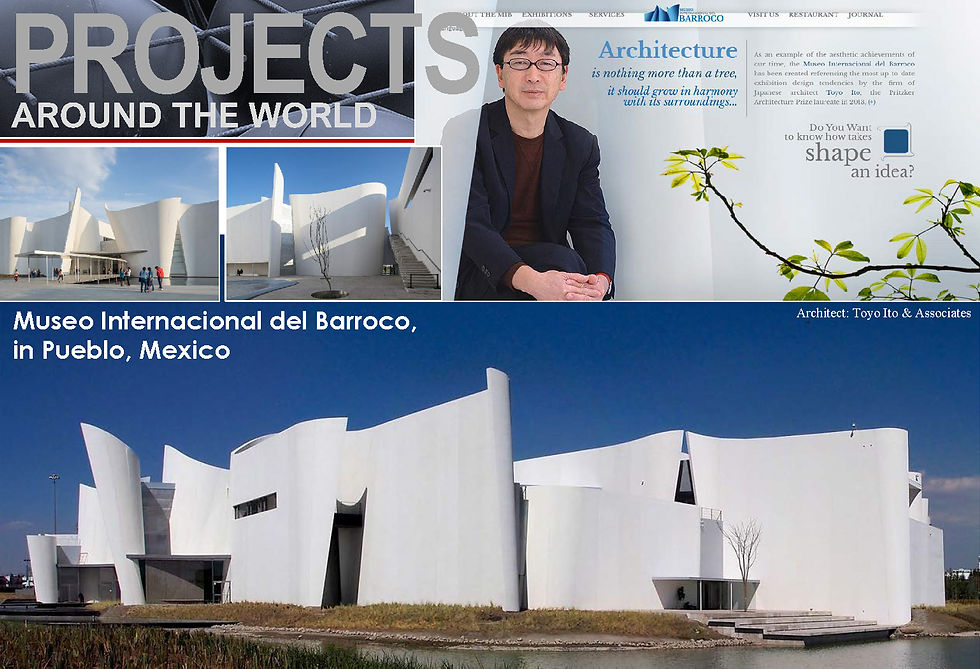
PRODUCT
INFORMATION
BUBBLEDECK MAXIMUM INDICATIVE SPANS
The appropriate BUBBLEDECK slab version is engineered to suit building configuration, span length between supports, applied loading and vertical alignment of supports. Indicative spans, based on our standard Grade 35 concrete as guide to what can be achieved.
Maximum spans indicated are based on 35mm concrete cover to bottom rebar (2 hours fire resistance); live load 3+1 kN/m² and lightweight external envelope maximum 6 kN/m line load. Completed slab mass and site concrete quantity based on 3m x 9m precast elements with 51 kg/m² total reinforcement.
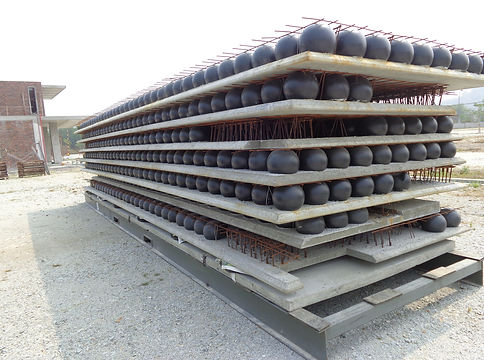
.jpg)




BD230
BD285
BD340
BD395
BD450

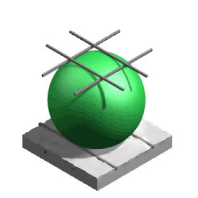


ELEMENT TYPE
LAUNCHING
& INSTALLATION
GREEN CREDENTIALS
BUBBLEDECK
SAVE THE EARTH STARTS WITH EVERYONE
Compared to a solid slab with the same thickness, BUBBLEDECK saves 35% of concrete in the slab and saves 50% with the same bearing effect. This will lead to further reductions through
the entire structure.
​
The production of one ton of cement causes an emission of
about 800kg of CO2. One m3 of concrete causes CO2 emissions close to 300kg. This figure does not even include emissions
due to quarrying, transport, etc.
​
Other GHG and natural resources (water, sand, stone)
are reduced proportionally.
BUBBLEDECK uses recycled plastic balls, and all materials
can be reused upon demolition.
​
Throughout the structure’s life-time, the envelope and
all internal work can be removed, and the original frame
simply refitted for a new purpose.
​​
The biaxial nature of BUBBLEDECK allows for any
internal layout to be reconfigured.

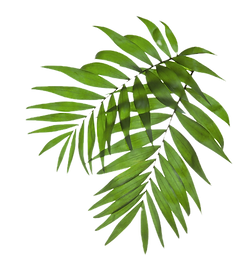
RESPONSIBILITIES
GREEN
SAVING THE EARTH NOW IS SAVING THE FUTURE FOR OUR CHILDREN
By reducing the amount of concrete in the middle of a slab, BUBBLEDECK makes a significant contribution to the environmental impact. Guidance from ODPM requires the direct environmental effects of building to be considered, including usage of natural resources and emissions resulting from construction. Not only is concrete usage reduced up to 50% within a building structure but the additional benefits, can be realized through reduced foundation sizes.
​
Every 5,000 m² of BUBBLEDECK floor slab can save up to:-
-
1,000 m³ site concrete
-
166 ready mix lorry trips
-
1,798 tonnes of foundation loads
-
416 million Kcal energy used in concrete production and haulage
-
278 ton of CO² - green house gas emissions.
LESS CONCRETE
Every 1kg of recycled plastic balls saves 100kg of concrete.
LESS CARBON DIOXIDE (CO2)
Saving of up to 40kg CO²/m². A 50,000m² building can save up to 2,000MT of CO².
MINIMUM FORMWORKS REQUIRED
A 50,000sqm of BUBBLEDECK will save 250 trees.
LESS FOUNDATION
Lower loading on the entire building. Less Excavation work for basement.
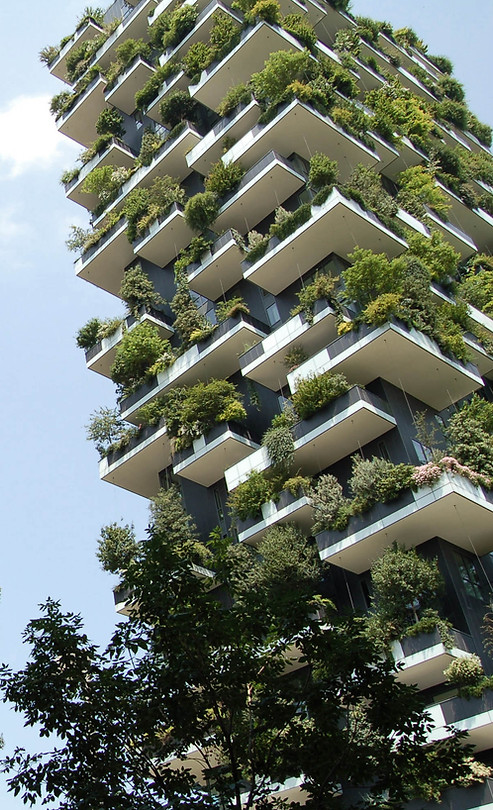
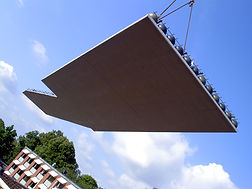
BUBBLEDECK FAQ
-
Who is the founder of the BubbleDeck system? Professor Jorgen Breuning.
-
How long has BubbleDeck system been in the market? More than 30 years.
-
Where was BubbleDeck system originally from? Denmark.
-
Where is BubbleDeck International principal office location? Rösevangen 8, DK 3520 Farum.
-
Which countries has BubbleDeck system landed? More than 40 countries around the world.
-
Which country has the most BubbleDeck projects up to to-date? The Netherlands and Australia.
-
Where is the tallest BubbleDeck project? How tall? Italy. 209-meter height.
-
What does BubbleDeck International do?
-
Combining international activities
-
Supervising the technical support/education
-
General quality supervision
-
Carrying out specialised tasks/projects
-
Developing new techniques
-
Developing new markets
THE BUBBLEDECK PRINCIPAL
THE BUBBLEDECK SYSTEM
-
What is BubbleDeck? BubbleDeck System is a revolutionary construction method by eliminating concrete from the neutral axis of a floor slab that is structurally not performing, as a result dramatically reducing in Dead Weight. The BubbleDeck System is based upon patented integration technique - the direct way of linking air and steel. Void formers inside the flat slab eliminate at least 30% of a slab’s dead weight. Incorporation of recycled plastic bubbles as void formers allows wider space between columns. Combination of this with a flat slab construction approach spanning in two directions - the slab is connected directly to in-situ concrete columns without any beams - produces a wide range of cost and construction benefits.
-
How does BubbleDeck work? The BubbleDeck system is based upon the patented integration technique - the direct way of linking air and steel. By adapting the geometry of the ball and the mesh, optimised concrete construction is obtained, with the simultaneous maximum utility of both moment and shear zones. The construction literally creates itself as a result of the geometry of two well-known components: Reinforcement and hollow plastic balls. When the top and bottom reinforcement are linked in the usual way, a geometrical and statical stable BubbleDeck unit evolves. The reinforcement catches, distributes and locks the balls in an exact position, while the balls shape the air volume, control the level of the reinforcement, and at the same time stabilise the spatial lattice. When the steel lattice unit is concrete, a “monolithic” biaxial hollow slab is obtained.
-
What are the major materials for the BubbleDeck system? Concrete, Wire Mesh, Steel Bar, Plastic Bar, Lattice Girders.
-
What are the Advantages of the BubbleDeck system? Please refer to the "ADVANTAGES".
-
Is there any warranty on the BubbleDeck system? Yes.
-
What does BubbleDeck Warranty cover? Concrete Product Warranty and Product Technology Warranty.
-
Is BubbleDeck fireproof/resistant? Yes, it’s tested and certified by SIRIM. For more information, please refer to OUR ASSURANCE.
-
Is BubbleDeck soundproof/resistant? Yes.
-
Is BubbleDeck earthquake-proof / resistant? Yes, the seismic design can be incorporated upon request.
-
Is BubbleDeck waterproof/resistant? Yes, it behaves the same as a conventional concrete structure.
-
Is BubbleDeck a structural element? Yes.
-
Is BubbleDeck required with Professional Engineer’s endorsement? Yes.
-
Is BubbleDeck slab system endorsed by Professional Engineer? Yes.
-
How many types of BubbleDeck slab system? 5 types. For more information, please refer to PRODUCT INFORMATION.
-
What is the thickness of the BubbleDeck slab system? Range from 245mm to 450mm.
-
Can the BubbleDeck slab float in the water? No, the BubbleDeck is not meant for floating in the water.
-
Is the BubbleDeck as strong as the conventional system? Yes, the strength is equivalent or higher compared to the conventional system.
-
Does other structural elements i.e. column and beam also has Bubbles inside? No
-
What is the function of the Bubble? The function of the Bubble is to replace the concrete that does not perform any structural function.
-
What is the material used for the Bubbles? The Bubbles are made of recycled plastic.
-
Does the Bubbles colour mean anything? No.
-
Are the Bubbles manufactured locally? Yes.
-
What structural impact would that be if the Bubble is damaged before construction? Usually, it doesn’t contribute any structural impact; it depends on the number of damaged Bubbles.
-
Can the Bubbles be sold separately? Yes, but it depends on the final purpose of using the Bubbles.
-
Is the BubbleDeck slab system suitable for landed housing? Yes.
-
Can tower crane be tied back to the BubbleDeck slab? Yes.
-
Is BubbleDeck slab system IBS certified? Yes.
-
Is BubbleDeck slab system contributing GBI points? Yes.
-
Does BubbleDeck slab system contribute to IBS score? Yes.
THE DESIGN & TECHNICAL
-
What is the Code of Practice for BubbleDeck slab system? EN13747.
-
What is the steel mesh standard for the BubbleDeck system in Malaysia? MS146.
-
What is the steel bars standard for the BubbleDeck system in Malaysia? MS145.
-
What is the weight of 1 piece of BubbleDeck slab? Approximately 2 ton to 4 ton, depending on the design.
-
Can the BubbleDeck slab system be designed for transfer floor? No.
-
Can there be any construction joints in BubbleDeck slab system? Yes.
-
Is BubbleDeck slab system allowed for seismic design? The BubbleDeck slab system can be designed according to the requirement by the client.
-
Can an opening be allowed at BubbleDeck slab system after construction? Yes, confirmation and approval must be obtained from BDCC.
-
Can drops be allowed at BubbleDeck slab system? Yes.
THE PRODUCTION & QAQC
-
Is the production/manufacturing process of the BubbleDeck slab certified with any QMS? Yes, it is certified with Quality Management System ISO 9001:2015.
-
How does BDCC ensure the concrete is up to the required standard? Internal – Cube Test on 7 days, 14 days, 28 days. External – Cube Test by 3rd party laboratory service provider.
-
How does BDCC ensure the steel component is up to the required standard? 3rd party testing is carried out on every batch of steel received.
-
What is the standard lead time required for the first delivery? 6 to 8 weeks from the date of receipt of Letter of Award and the down payment.
THE LOGISTICS & PROJECT MANAGEMENT
-
How to transport BubbleDeck slab to the site? By trailer.
-
How to load and unload BubbleDeck slab? By tower crane or mobile crane.
-
What is the floor cycle for an area of 800m² of BubbleDeck slab system? 6 days cycle per floor, with a team of 6 workers.
-
How many days can the scaffolding allow to be dismantled for BubbleDeck slab system? Upon the concrete achieved the characteristic design strength.
-
Is the launching and installation work for BubbleDeck slab system to be carried out by BDCC? Upon the client’s request and as per the agreed terms of sales.
-
Is site supervision provided by BDCC? Upon the client’s request and as per the agreed terms of sales.
-
Is the concrete topping work to be covered by BDCC after the BubbleDeck slab system has been installed at the site? No, under normal circumstances, it should be done by the others.